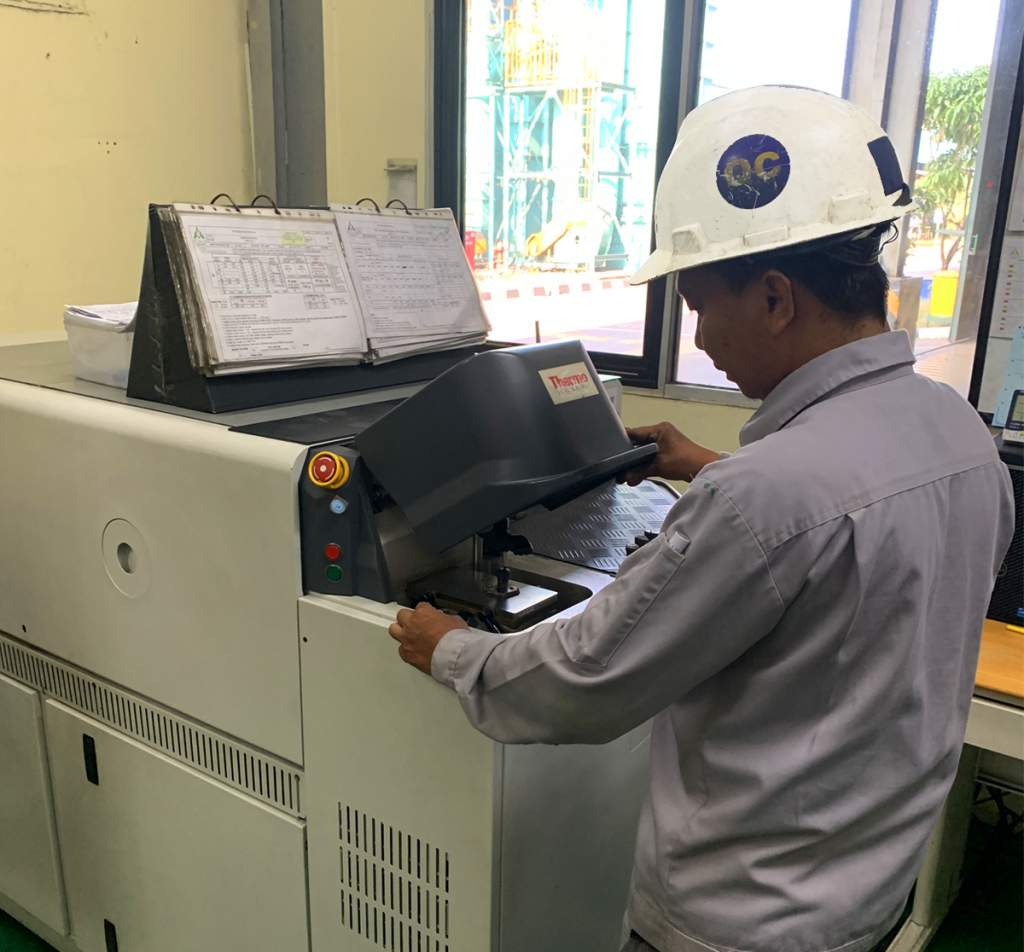
Quality assurance in a metal casting company involves monitoring and controlling the quality at every stage of the casting process to ensure the final product meets specification and performance standards. The quality assurance team regularly conducts inspections and tests on raw materials, molds, and final components to detect defects and ensure compliance with industry standards. Quality assurance procedures also include implementing strict documentation and reporting systems to track test results and necessary improvements.
MATERIAL CHECK
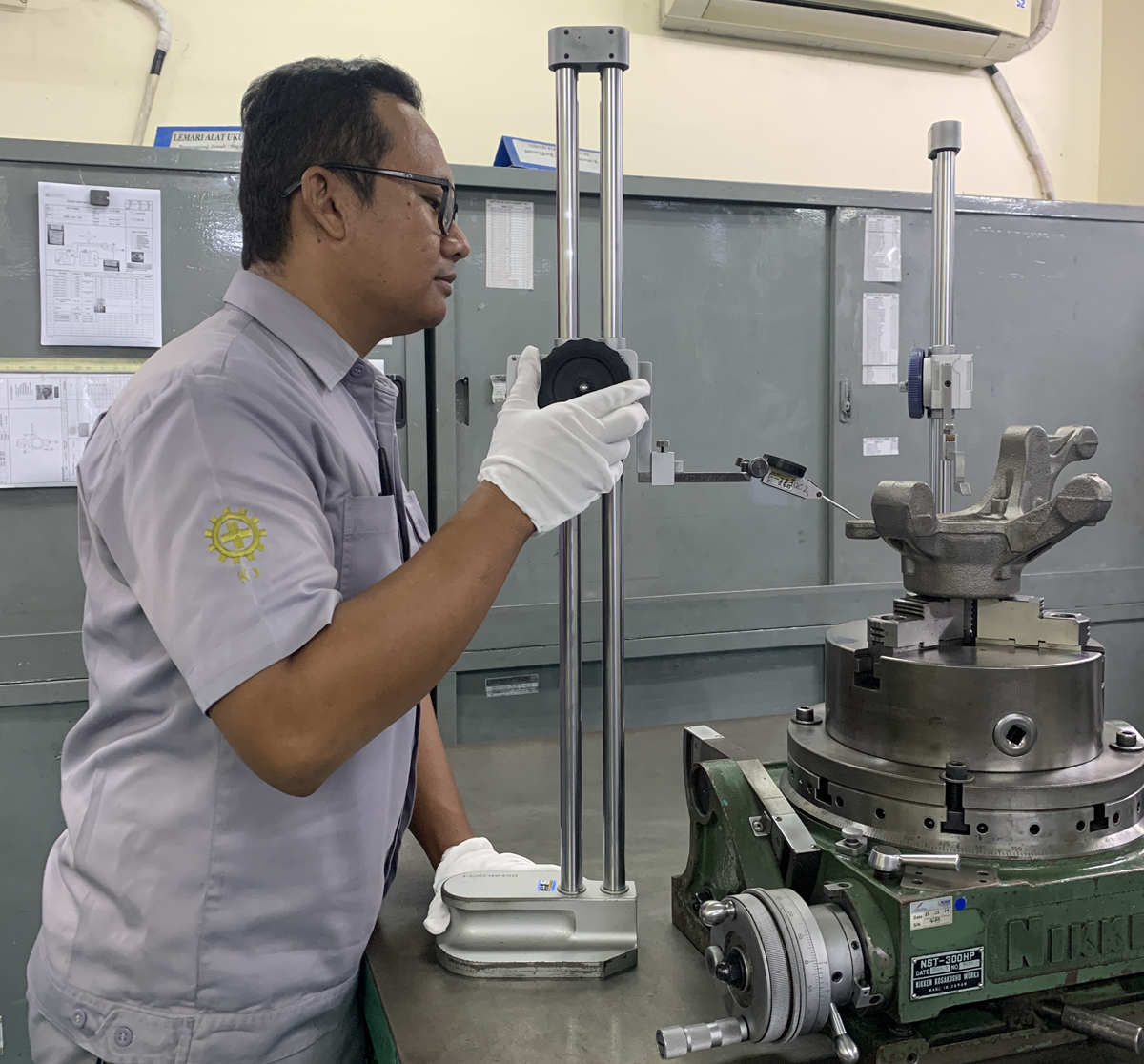
MEASURMENT CASTING MATERIAL
Precision measuring instruments are used to ensure accurate and detailed measurements in the metal casting process.
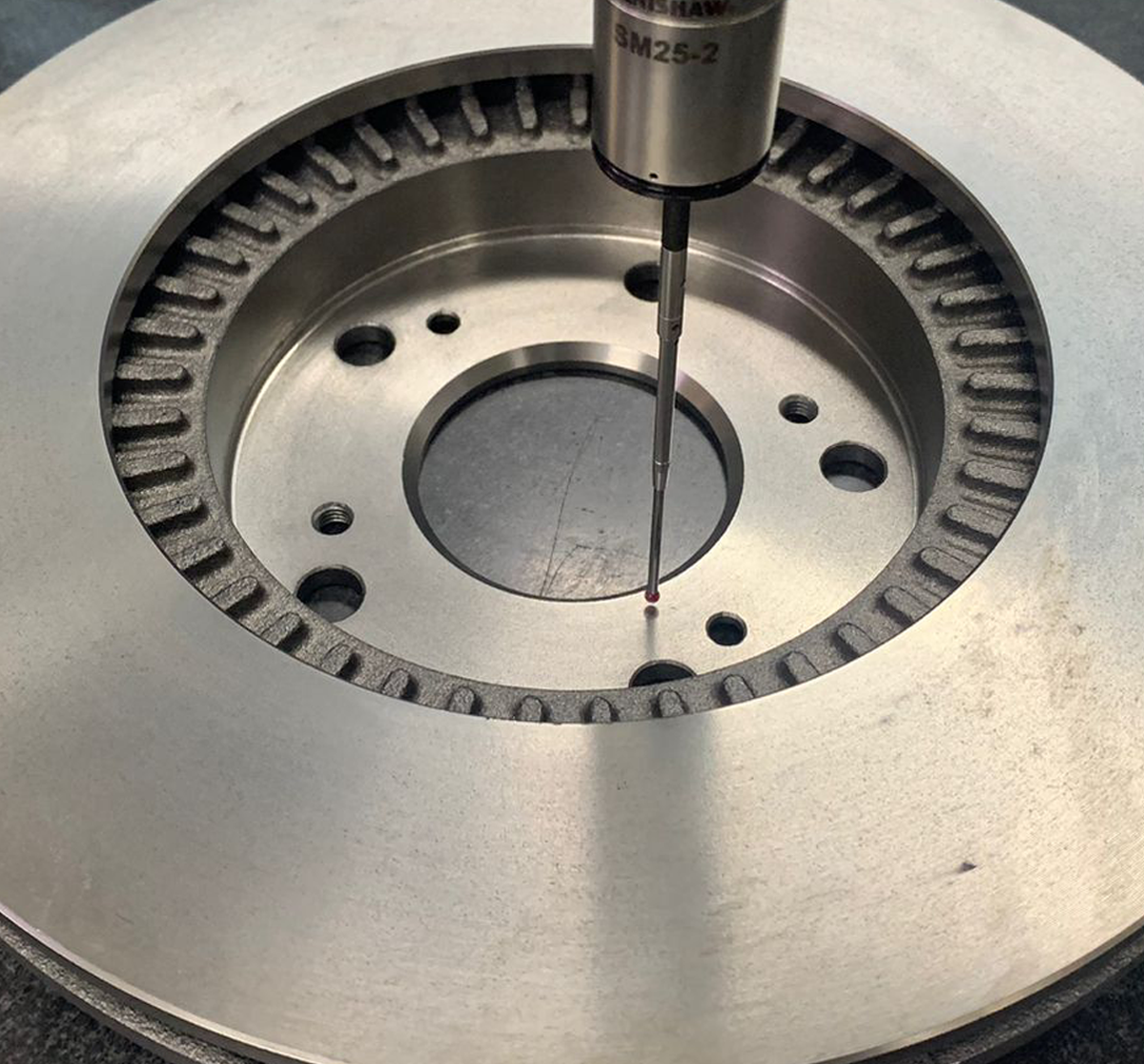
COORDINATE MEASURING MACHINE
Automated measurement using advanced technology ensures accuracy and consistency of component dimensions in the metal casting process
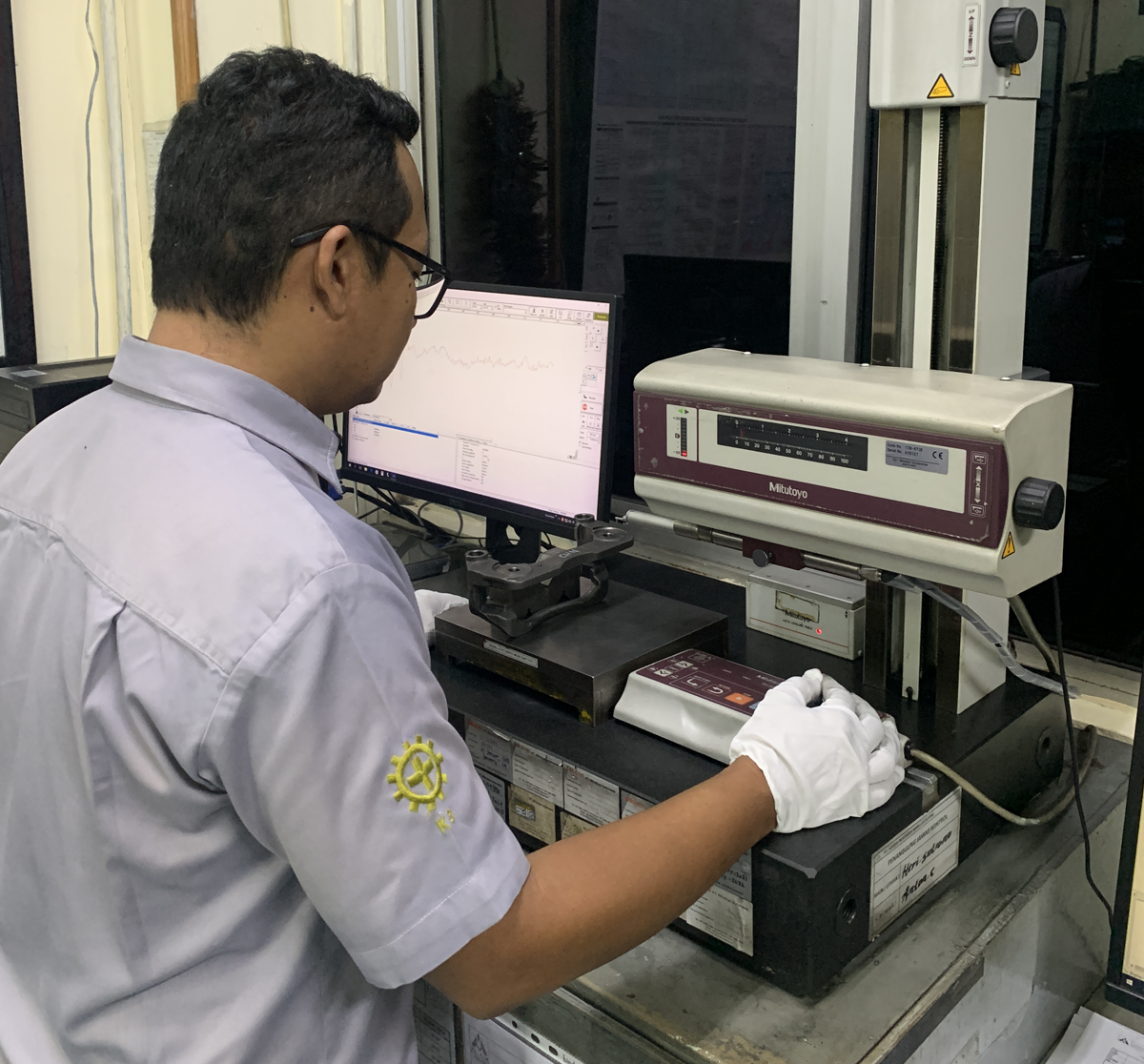
CONTRACER MEASURING MACHINE
The contracer machine precisely measures and analyzes the profile and contour of a workpiece by recording height changes, ensuring the results meet specified requirements.
STRUCTUR ANALYIS
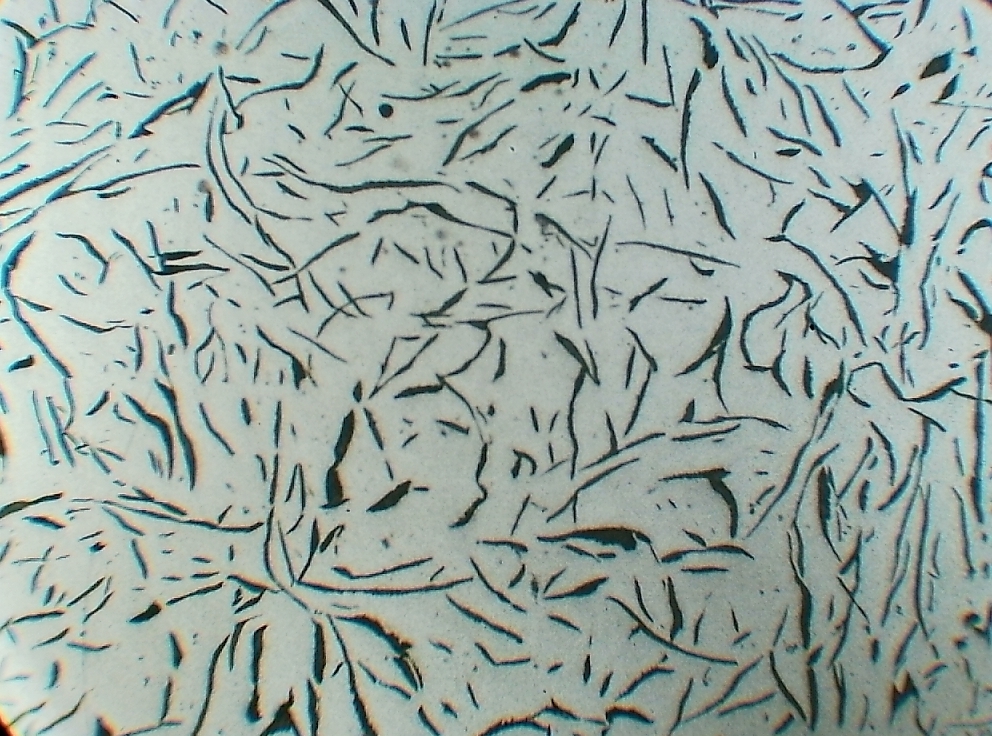
MICROSTRUCTUR ANALYIS
The results of material analysis are used to determine the characteristics of the material, such as chemical composition and mechanical properties, to ensure its suitability with production standards in the metal casting process.
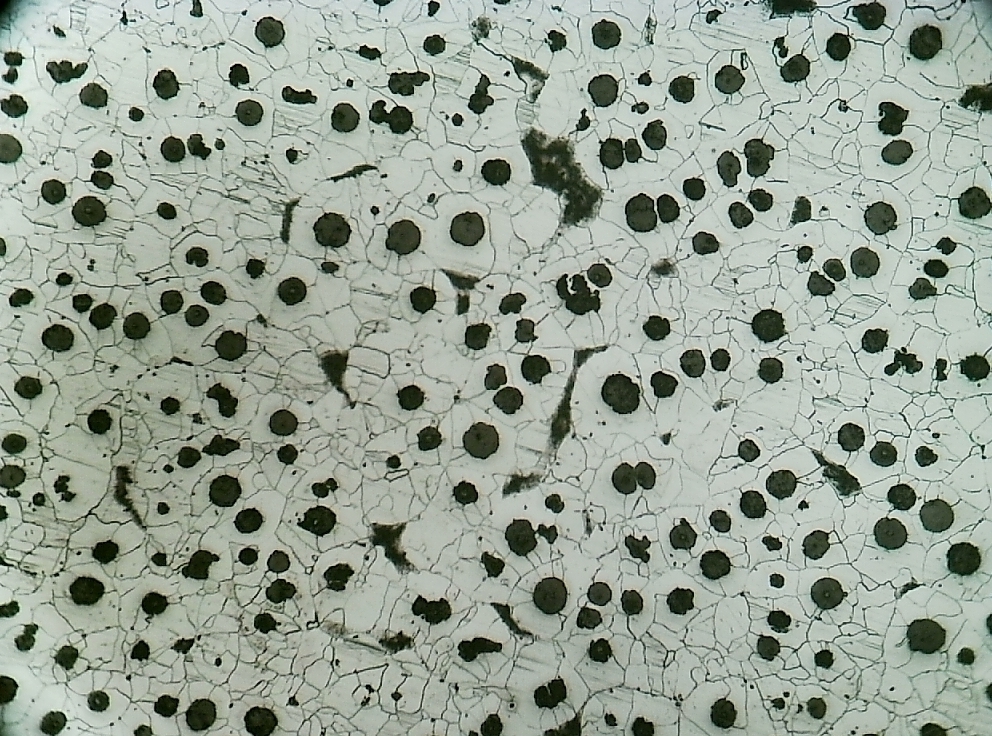
MICROSTRUCTURE ANALYIS
The results of material inspection are used to ensure that the materials meet the required technical specifications and quality standards before being used in the metal casting process.
INSPECTION EQUIPMENT
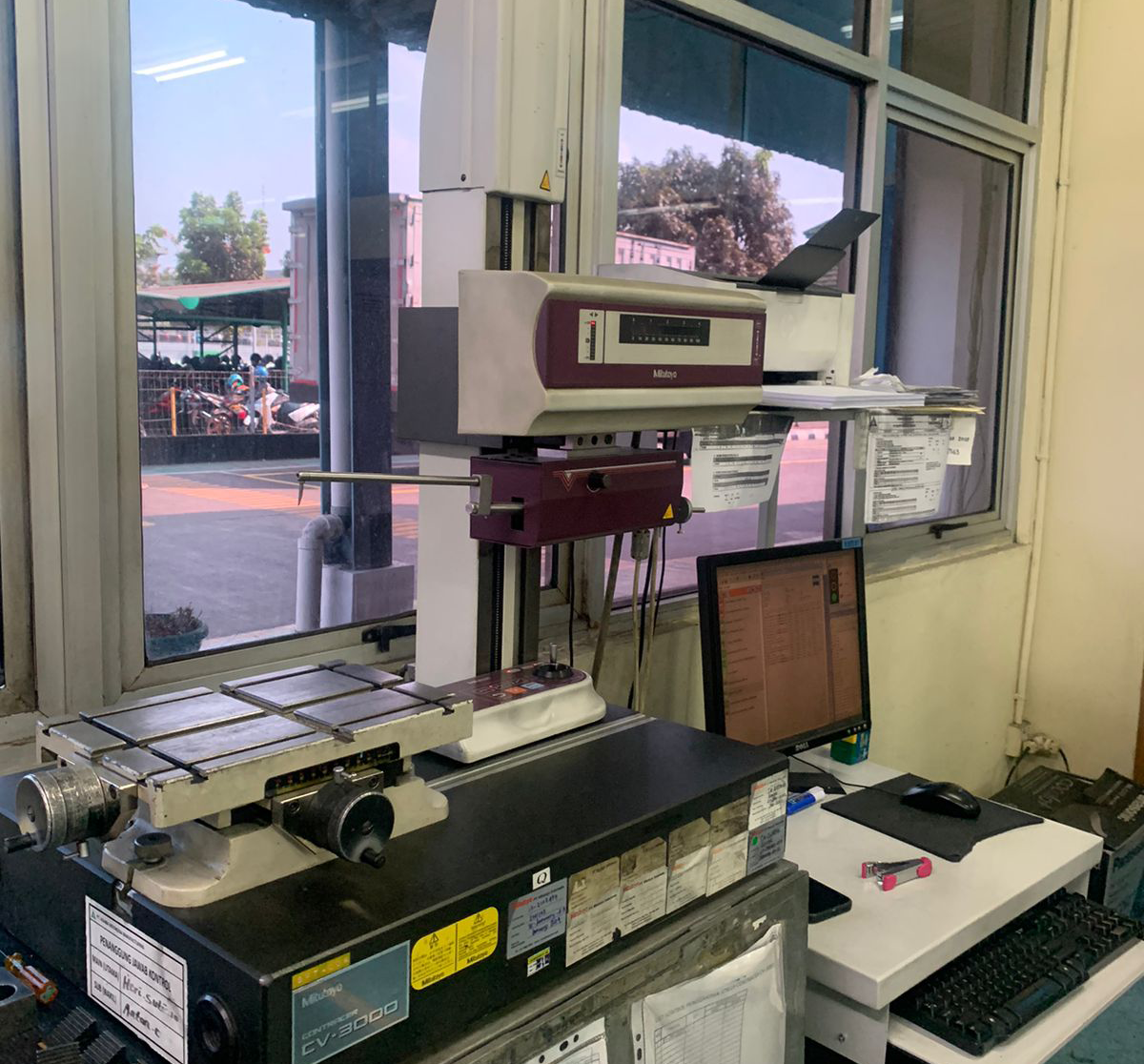
CONTRACER MEASURING MACHINE
The function of a contracer is to measure and analyze the surface profile of components with high precision, ensuring quality and conformity to specified standards.
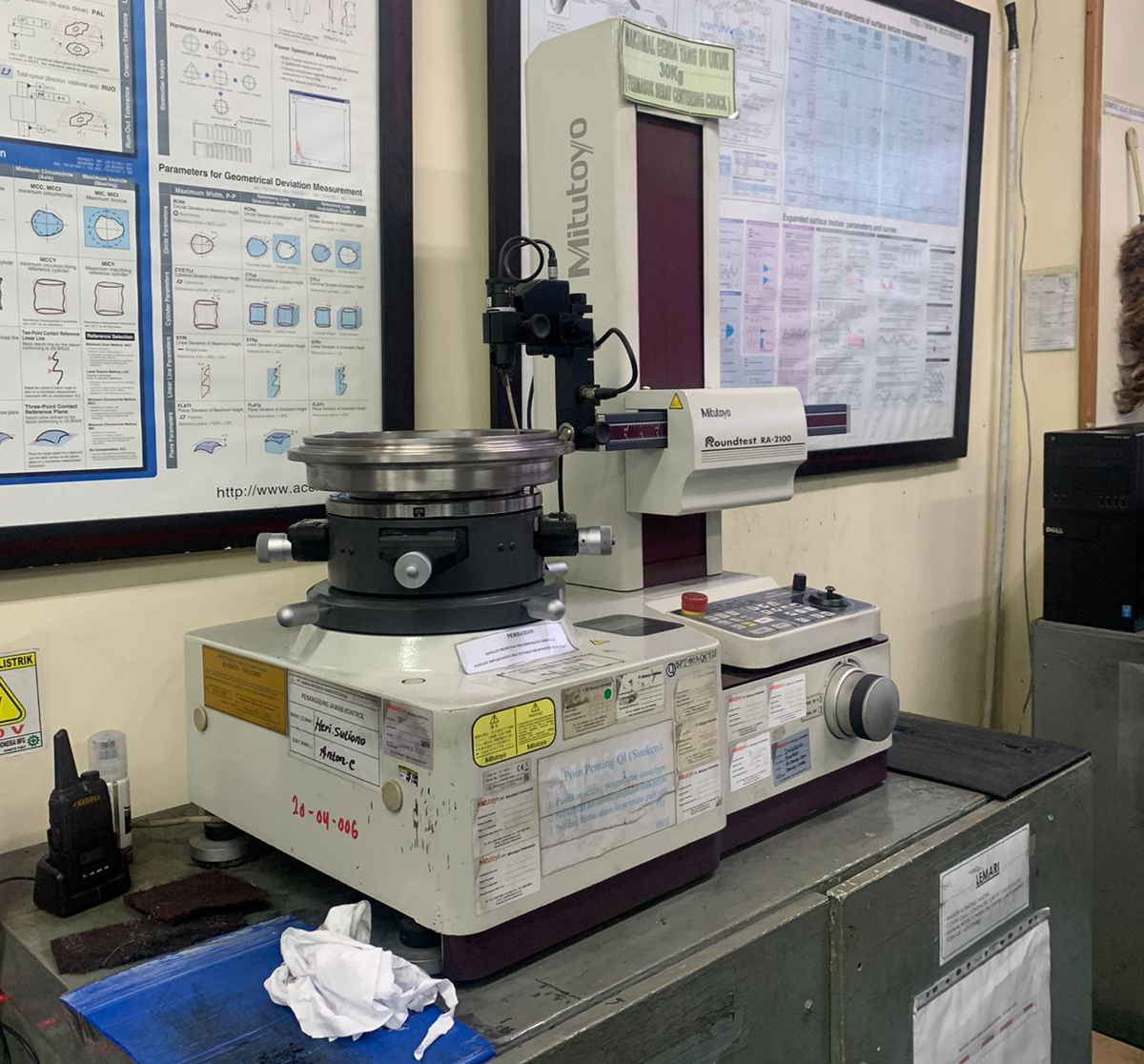
ROUNDESS MEASURING MACHINE
The function of a roundness tester is to determine the roundness of components with high accuracy, ensuring that the parts meet specified geometric tolerances.
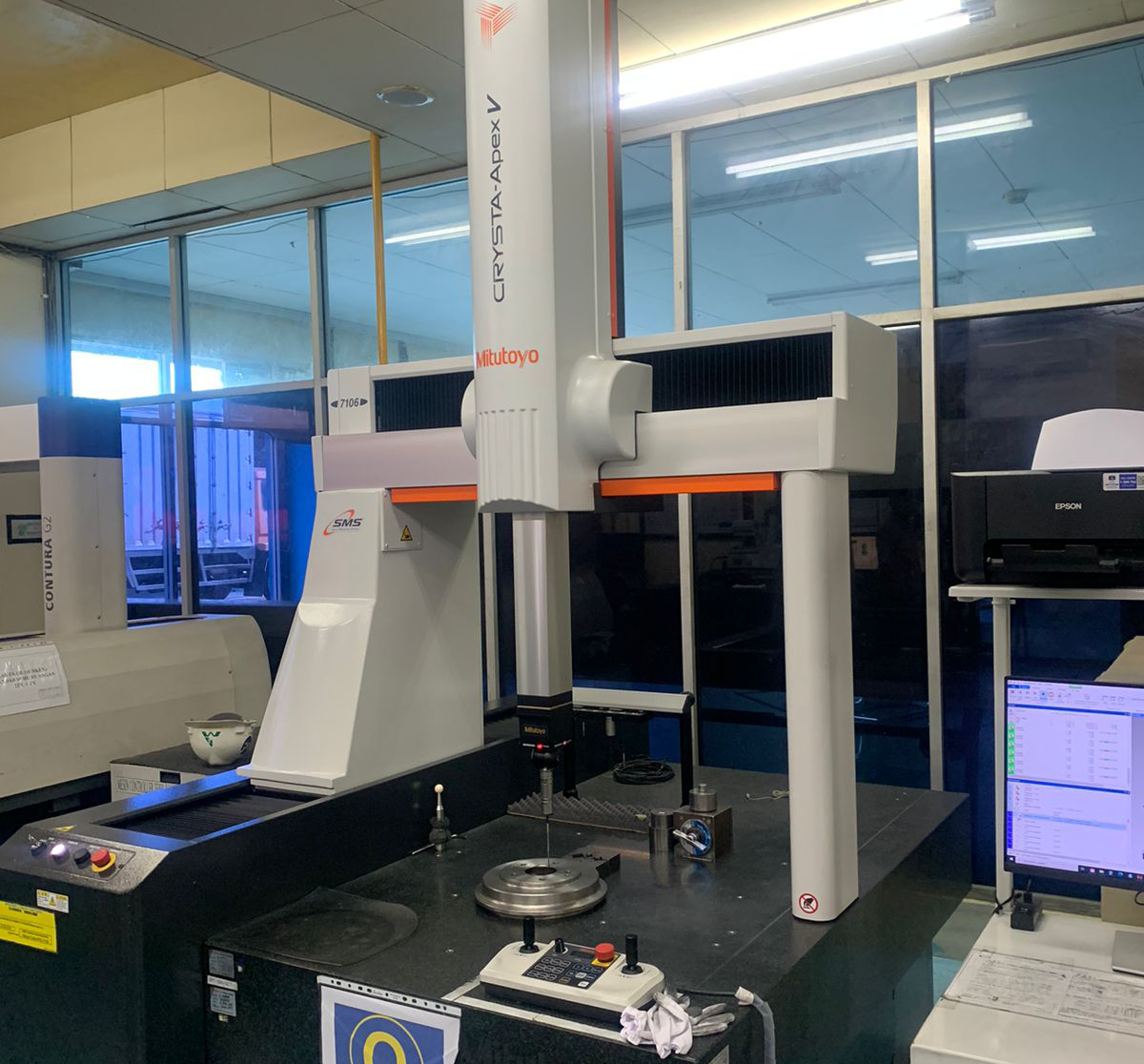
COORDINATE MEASURMENT MACHINE
The function of a CMM (Coordinate Measuring Machine) is to measure the physical dimensions of an object with high precision using three-dimensional coordinates, ensuring that components meet design specifications and tolerances.

STRENGTH TESTER
A strength test is used to measure the ability of a material or component to withstand load or stress without failure, ensuring its reliability in specific applications.
SCREEN MONITORING
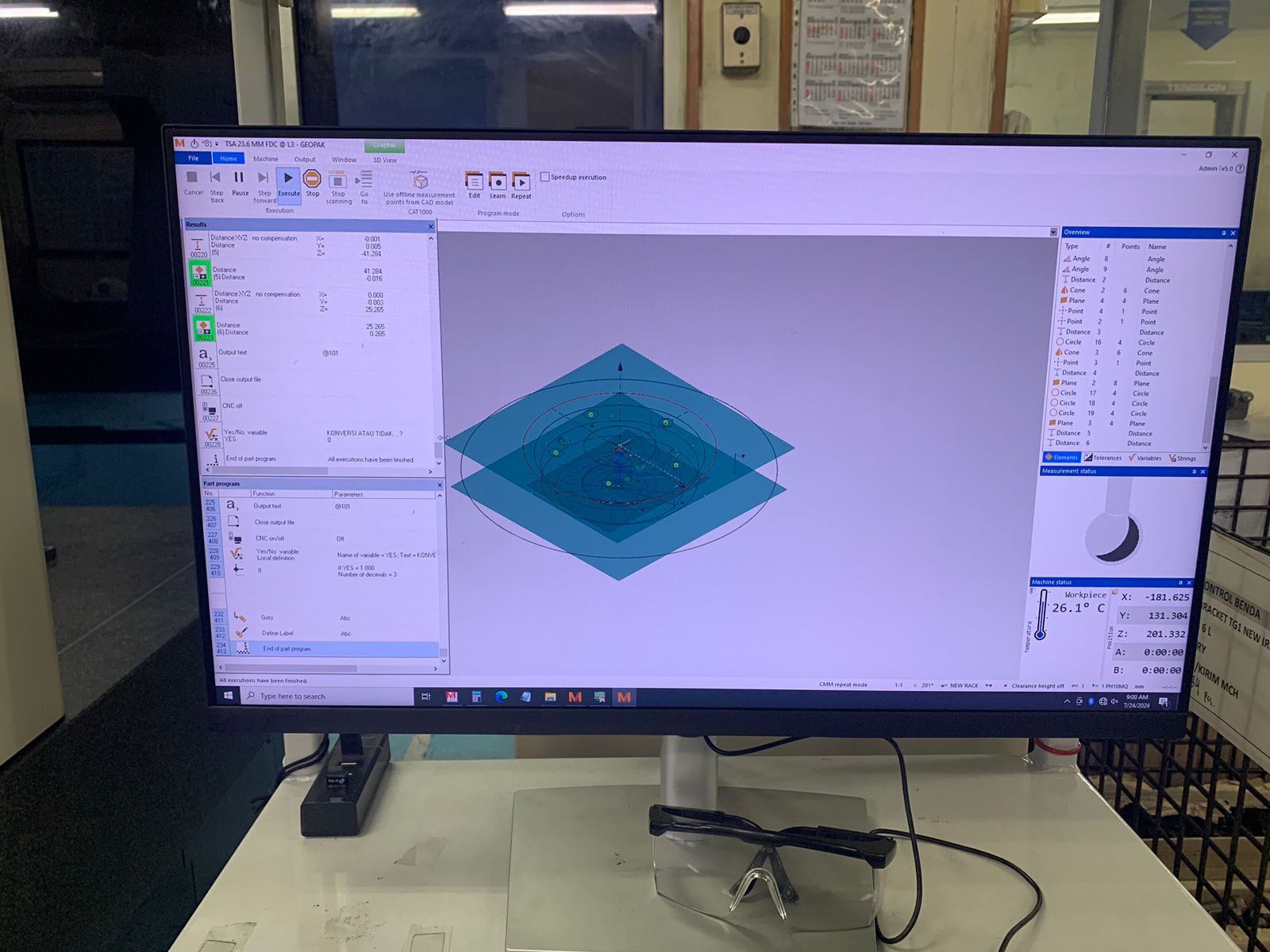
CMM Monitoring
The results from a Coordinate Measuring Machine (CMM) provide accurate data on the dimensions and geometric features of a workpiece, ensuring they meet the specified tolerances and design requirements.
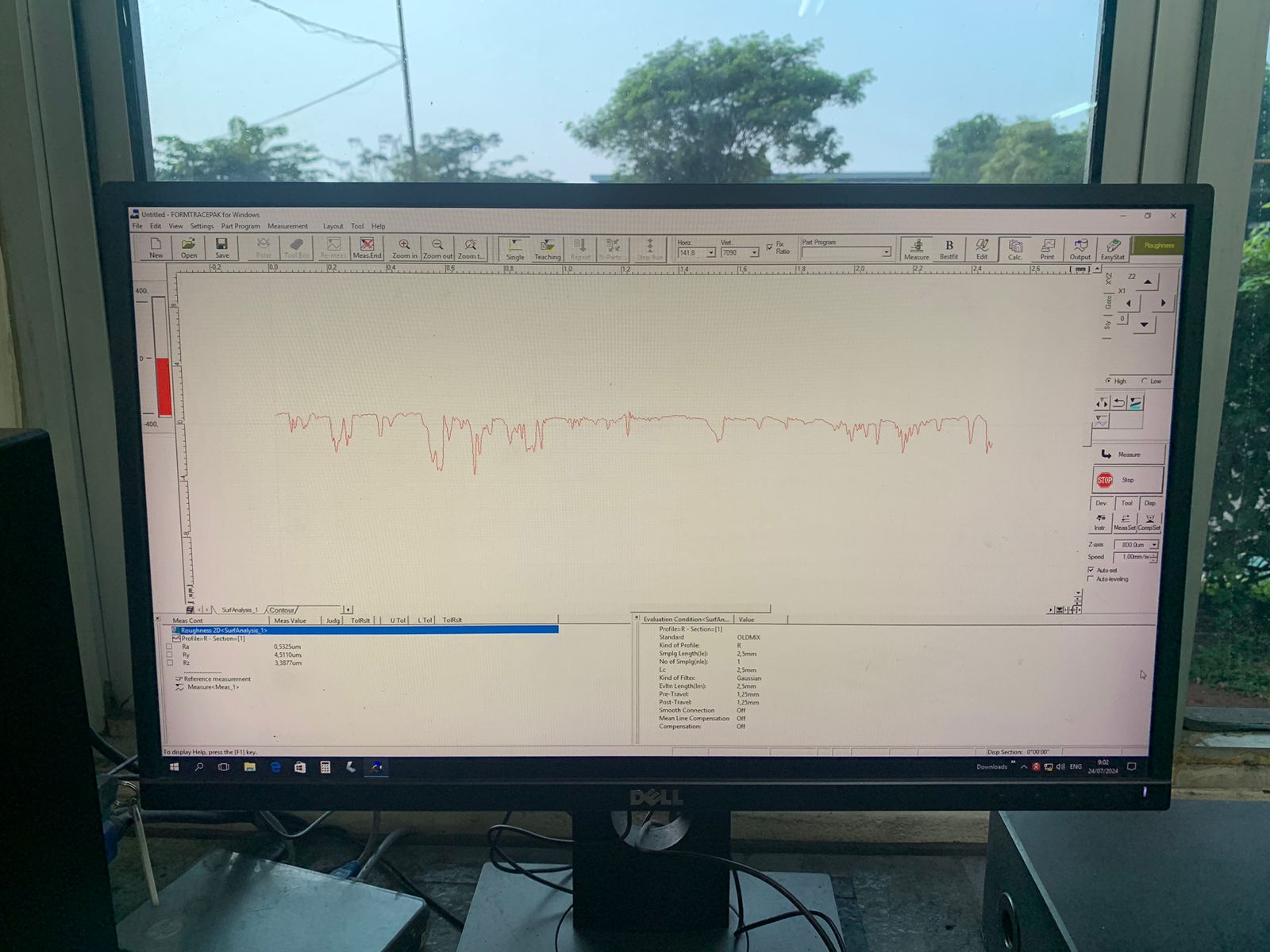
Contracer Monitoring
The measurements from a contracer machine provide detailed information on the contour and profile of a workpiece’s surface, ensuring that its dimensions and shape conform to the established standards.
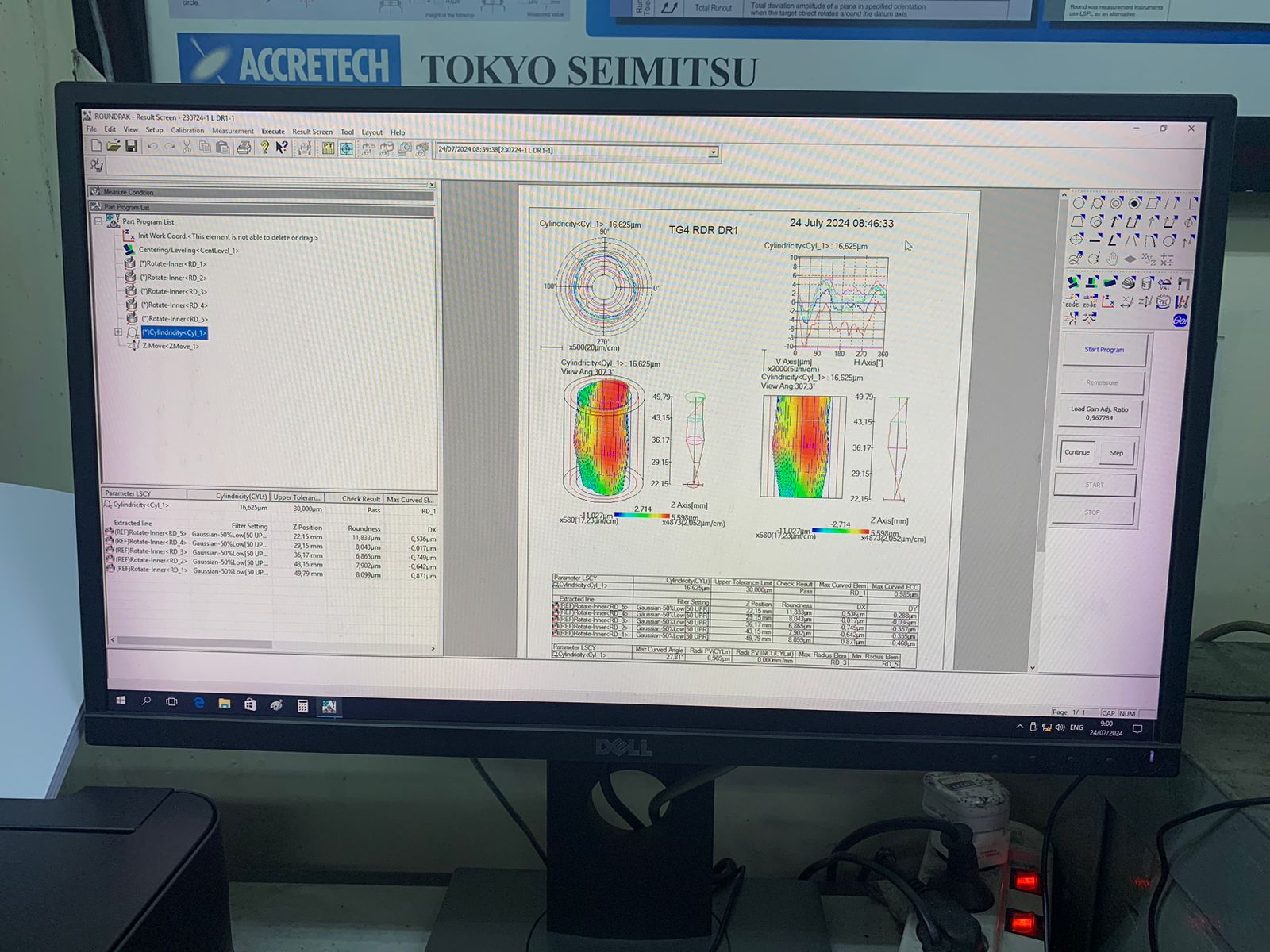
Roundess Monitoring
The results from a contracer machine can also provide data on roundness errors of a workpiece, ensuring that its shape conforms to the allowed tolerances.