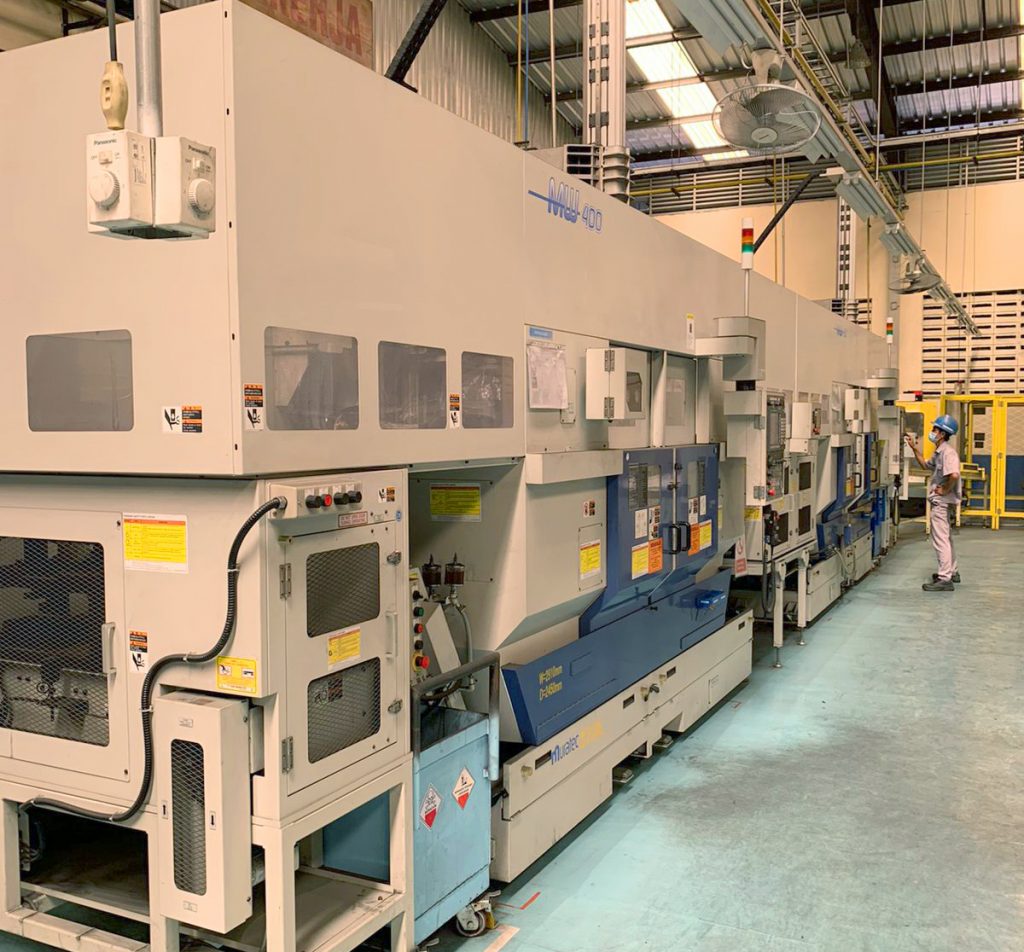
The machining process involves cutting and refining material to achieve the desired shape and size of metal components. During machining, cutting tools such as drills, mills, and lathes are used to remove material from the workpiece with high precision. This process requires careful adjustment of machine parameters to ensure surface quality and accurate tolerances. Machining is often used to produce components with very detailed and precise specifications, as well as to repair and refine the final product.
Machining Line
- 12 units : CNC twin spindle lathe machine
- 33 units : CNC single spindel horizontal lathe machine
- 12 units : CNC single spindel vertical lathe machine
- 11 units : CNC machining center vertical machine
- 12 units : driling and tapping machine
- 7 units : driling machine
- 4 units : vanishing machine
- 8 units : honing machine
- 2 units : 4 axis single way special machine
- 2 units : 10 axis double way special machine
- 1 unit : hole pin 3 spindle machine
- 7 units : washing machine
- 8 units : balancing machine automatic
- 1 unit : painting machine
- 1 unit : painting cathodic electro deposition (CED)
- 1 unit : drying machine
- 2 units : magnetizing machine
- 1 unit : assembling machine diff
- 2 units : hydraulic press machine
- 6 units : stamping machine
- 1 unit : flywheels machine
- 3 units : broaching machine
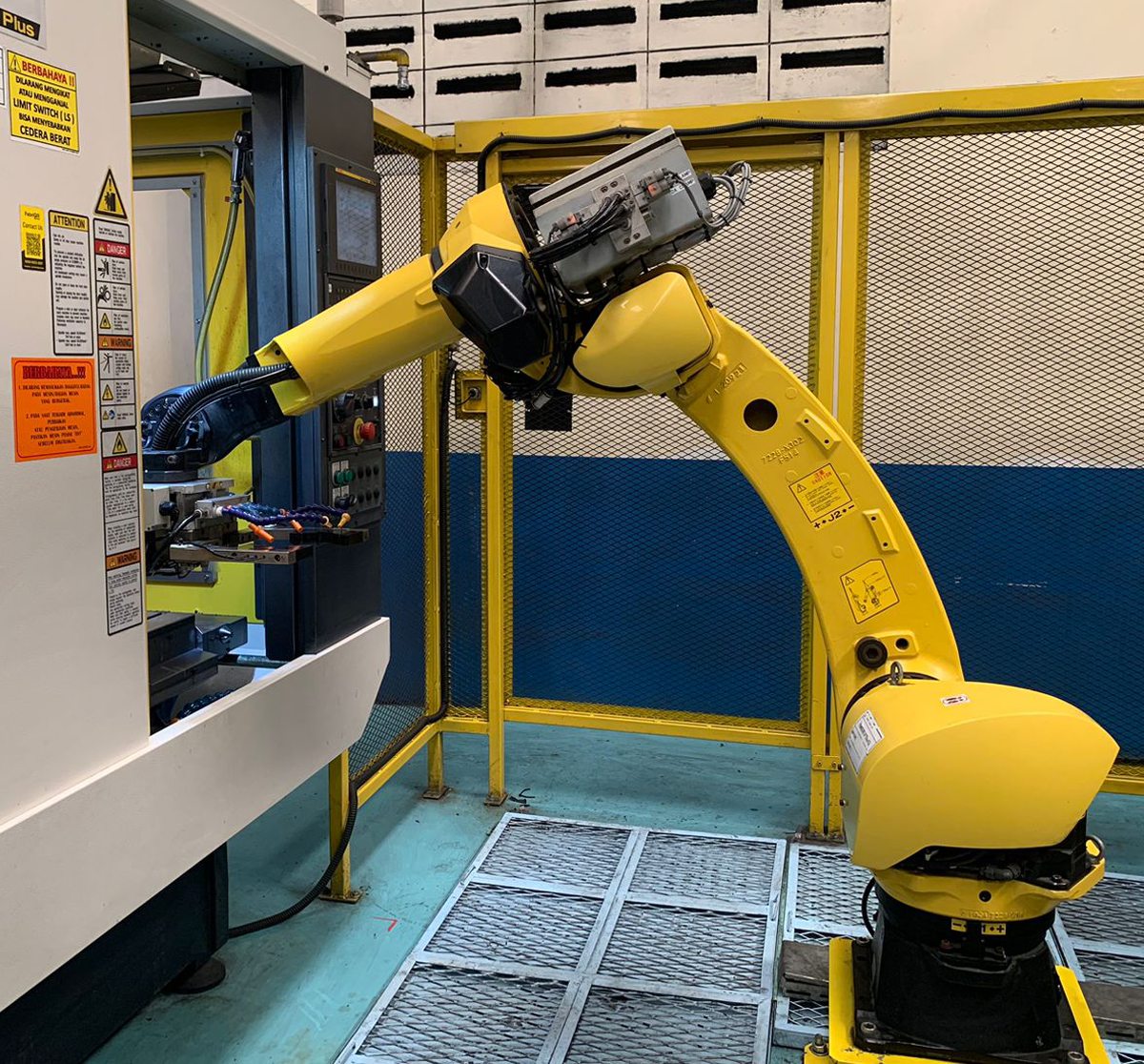
Automatic CNC machine with a robotic arm handling the in-and-out movements of materials, ensuring precision and efficiency.
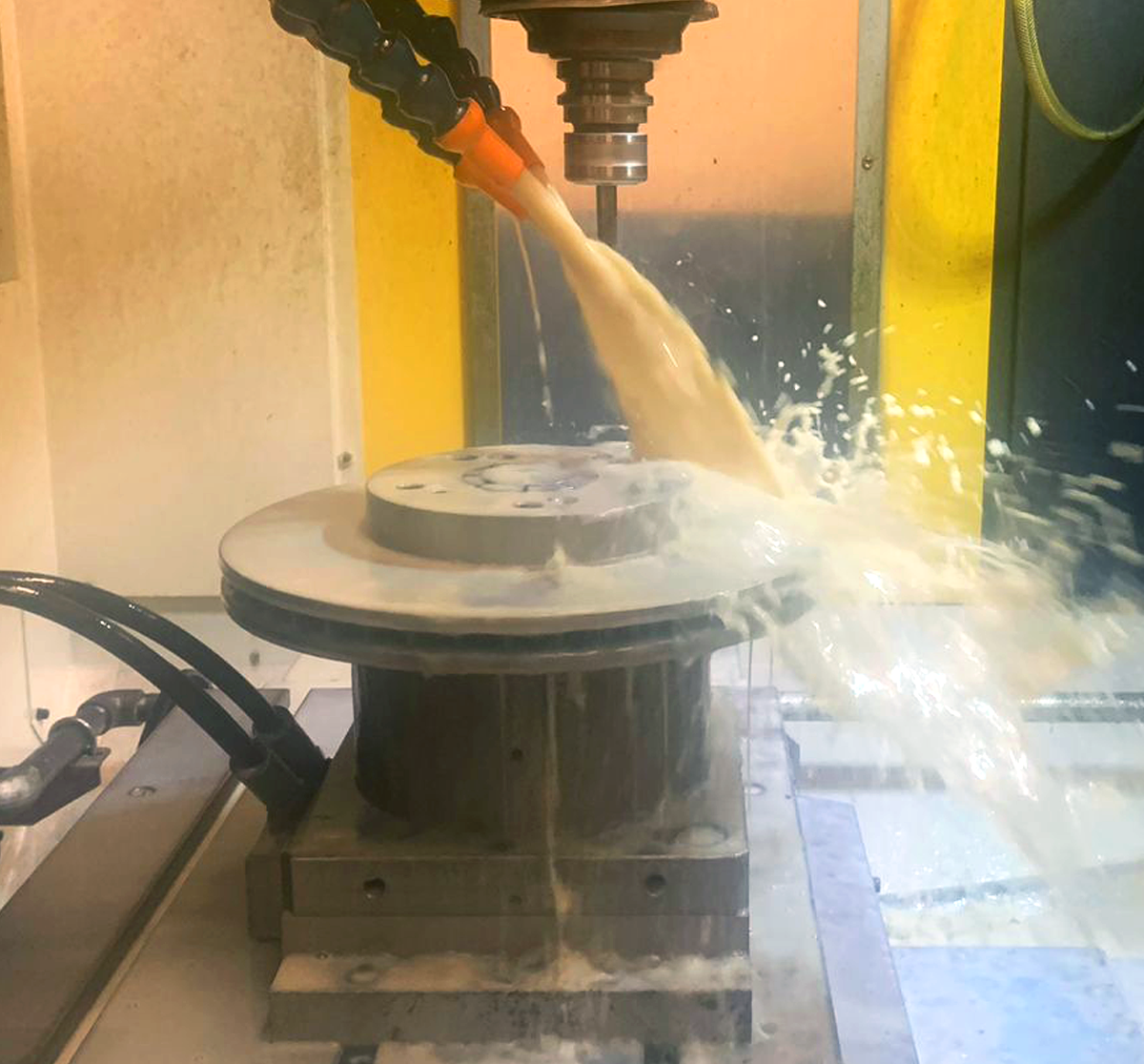
Automatic CNC machine running without an operator, showcasing seamless precision and efficiency
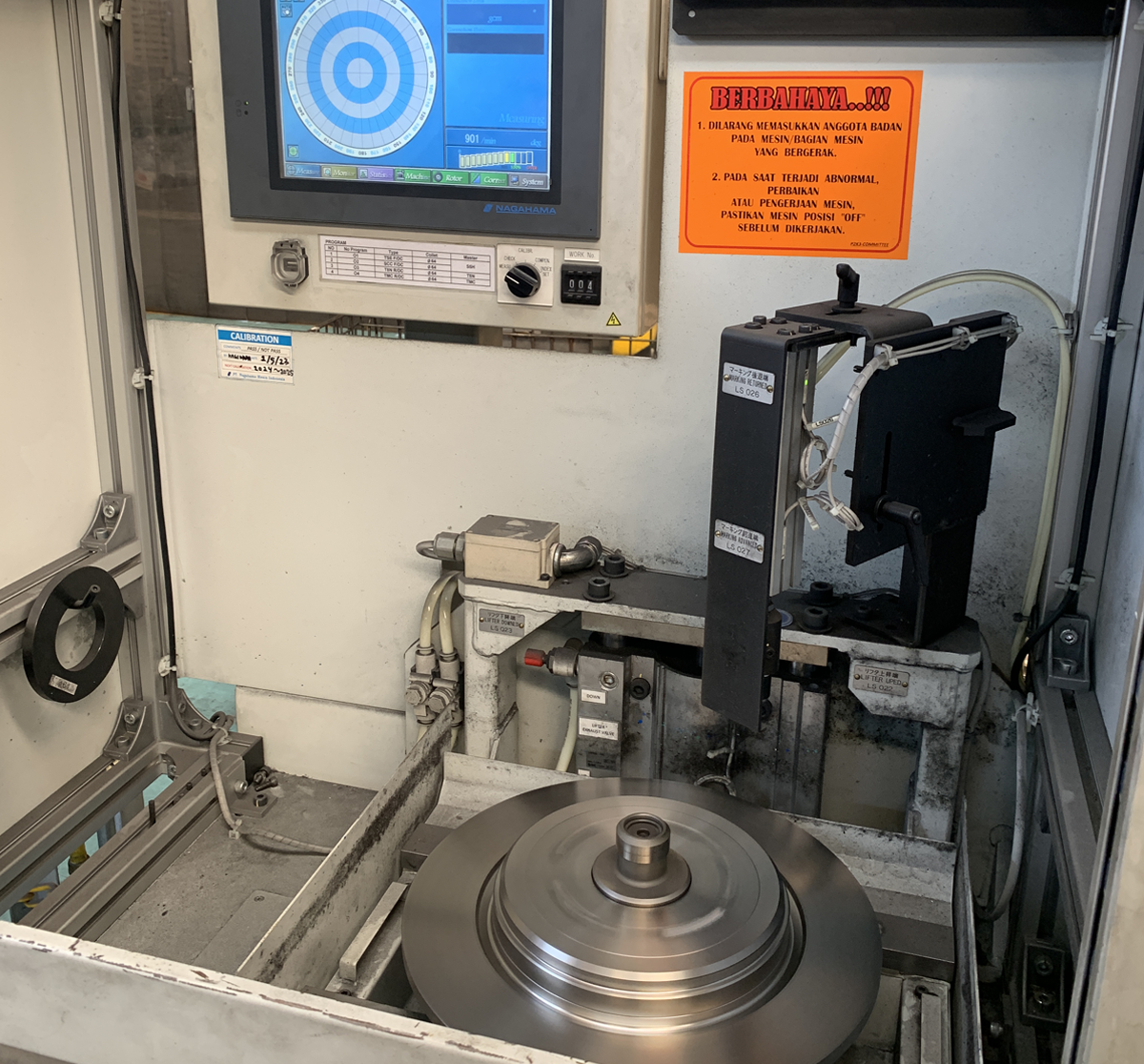
A balancing machine is used to check the precision of disc and drum parts by detecting and correcting imbalances.
The crack detection process using anti-crack sensors involves monitoring and inspecting materials to ensure there are no hidden damages. In this process, specialized sensors such as ultrasonic, optical, or acoustic sensors are used to detect cracks in the workpiece with high precision. These sensors require careful adjustment of parameters to ensure surface quality and accurate crack detection. Crack detection is often used to ensure that components have very detailed and precise specifications, as well as to inspect and refine the final product.
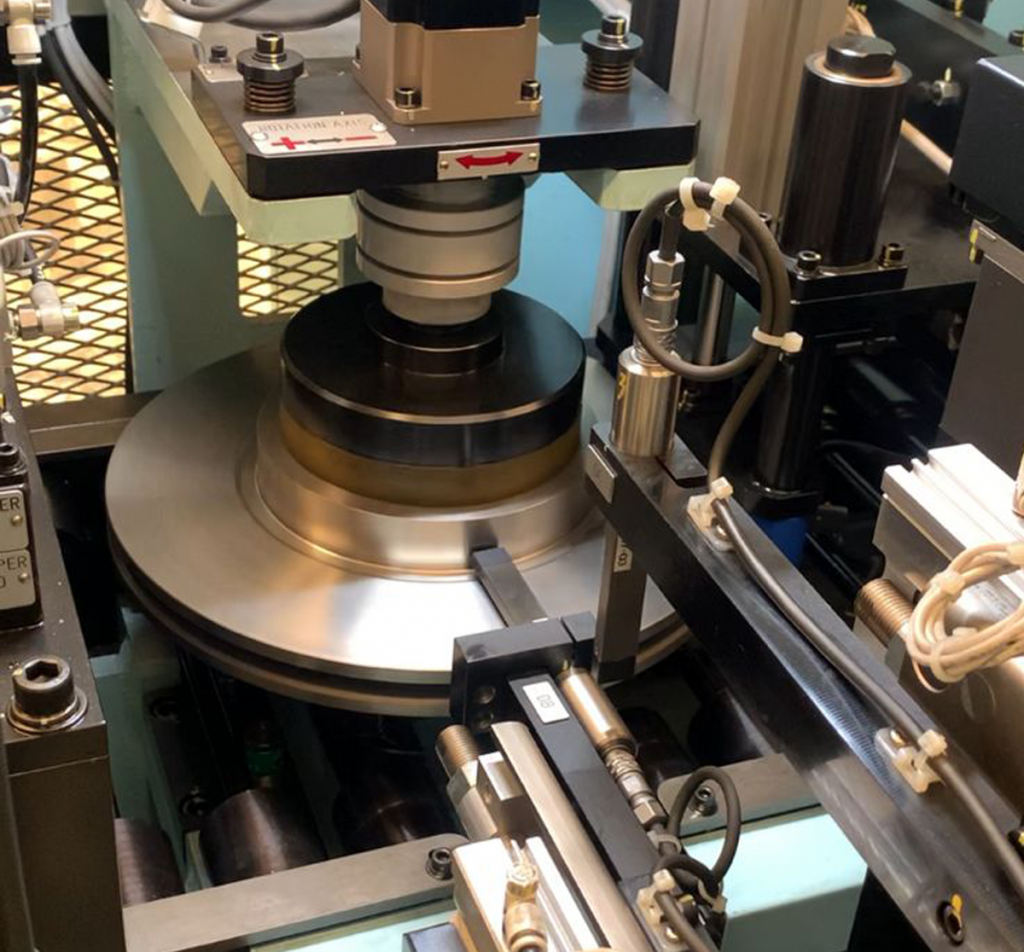